生産技術がいつも先行するイノベーション、設計は?
生産技術は、設計に比べて常に革新されている印象がありませんか?コストや時間や様々なリソースに直接関係することと、利用者へ提供される製品を生産しているわけですから、いろんな確度からコストを下げ、時間を短縮し、品質を上げる活動がなされるのは、当然のことだといえましょう。
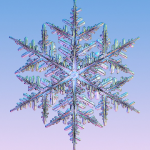
翻って、設計には革新技術がかなり遅れて登場してくるように思われます。成果も、生産のように直接見えることがなかったり、効果測定自体が難しかったりしますので、どうしても、目立たないのですね。とはいえ、生産のコストや品質を左右するのは設計なのですから、設計革新がないことには大きな製品改善は望めないのです。
過去にさかのぼって、代表的な生産技術革新と設計技術革新を対比した表を作成したので紹介しましょう。前からなんとなく気になっていて、けっこうアナロジーがあるように思っていたのですが、今回改めて整理してみると、設計が生産の後を追うようにして、似たような価値を追いかけてきている状況は想定以上でした。Innovationには、必ず淘汰されるコトやモノと新しい価値が存在し、これはほぼ一致するのですね。面白いですよ。
M1-D1の共通項:作業の複雑さを排除
生産ではベルトコンベアにより、作業の複雑さが排除され、大量生産ができるようになりました。それに対し、設計でも、図面を書いて試作する複雑さがCAD/CAEにより排除されたとみなせます。登場の差は50年あります。
M2-D2の共通項:人為作業を排除
向上での産業ロボットにより、人為作業がなくなり自動生産が可能になりました。設計の世界にもソフトウエア・ロボット(本ページでなんどか紹介)が誕生したことで作業と計算の自動化が進みましたが、産業ロボットの30年後でした。
M3-D3の共通項:不良製品と不良設計を排除
不良製品を極力なくするための品質管理は第二次大戦での大量生産のころに産声をあげ、1950年代から開発されました。タグチメソッドやシックスシグマに代表されるロバスト設計は、不良設計をなくするための革新的な手法として、30年遅れて1980年代に登場します。
M4-D4の共通項:在庫削減とデータ滞留(データ在庫)のゼロに
JITはトヨタ生産システムのなかで採用された、在庫を減らして多品種少量生産に対応するための物流革新でした。設計プロセスにPLMが採用され、設計データを溜めるのではなく、流して次のプロセスにつなげていくという考えがでてきたことで、複雑性設計への対応ができるようになりました。JITの20年後です。
M5-D5の共通項:生産準備時間と設計検討時間をゼロに
IoTが工場に適用されたことで、製造装置間でデータの標準化進み、生産準備時間を大幅に短縮する受注生産が可能になりました。Zero Design Cycle Timeは、P&W社で実施されている事前設計探索を可能にするしくみです。設計案の検討時間をゼロにするという大胆な価値をもたらしています。IoTの10年後の技術です。
M6-D6の共通項:故障や保守時間という無駄を排除し、無駄な計算や検討を無くする
IoT for Serviceでは、製品の運用情報を常に監視することで故障や保守時間を最小にし、結果として稼働率を最大にするサービスが可能になります。シミュレーション・ビッグデータを活用することで、過去データからの知見を得ることができ、無駄な計算や検討を排除することができます。最大効率設計と命名すると、生産側の製品稼働率最大化とうまく対応します。ようやく、5年程度の差で設計技術が追いつくようになってきたようです。
さて、どうでしょう、多少無理にこじつけたところもありますが、生産と設計の革新技術が実にほぼ同じ順番で、似たような淘汰と新価値創造を試みていることがわかりますね。それに、登場する年代差も、50年から、ほぼ10年ずつ縮まってきて、いまでは5年ほどにまでに近づいています。設計革新もどうにか、生産のスピードに追いつきつつあるようにも見えますが、最先端のD5/D6はまだ一部の企業だけであったり、ようやく端緒に付いたばかりでもありますので、適用レベルではまだまだ差があるであろうと思われます。ともあれ、技術革新の動向をこういう視点で眺めて見るのも面白いでしょう?
*本記事は、Facebookページ「デザイン&シミュレーション倶楽部」および「ダッソー・システムズ株式会社公式ブログ」と提携して転載されております。